En el mundo de la electrónica en rápida evolución, la demanda de componentes de alto rendimiento, compactos y confiables es cada vez mayor. Uno de esos componentes que ha ganado un impulso significativo es el circuito impreso flexible multicapa (FPC). Este artículo explora las complejidades de la fabricación personalizada de FPC multicapa, centrándose en especificaciones como el acabado de la superficie, el espesor de la placa y el proceso de fabricación, particularmente en el contexto de los campos de cables con pantalla de prueba.
Comprensión del FPC multicapa
Los FPC multicapa son esenciales en los dispositivos electrónicos modernos y proporcionan una solución ligera y flexible para diseños de circuitos complejos. A diferencia de los PCB rígidos tradicionales, los FPC multicapa se pueden doblar y torcer, lo que los hace ideales para aplicaciones en teléfonos inteligentes, dispositivos portátiles y otros dispositivos compactos. La capacidad de personalizar estos productos permite a los fabricantes cumplir requisitos específicos, garantizando un rendimiento óptimo en diversas aplicaciones.
Productos personalizados: adaptación a necesidades específicas
La personalización es el núcleo de la fabricación de FPC multicapa. Cada proyecto puede tener requisitos únicos según la aplicación, como tamaño, forma y rendimiento eléctrico. Los fabricantes trabajan en estrecha colaboración con los clientes para desarrollar soluciones personalizadas que cumplan con sus especificaciones. Esta colaboración a menudo implica discusiones detalladas sobre el uso previsto del FPC, el entorno en el que operará y cualquier estándar regulatorio específico que deba cumplirse.
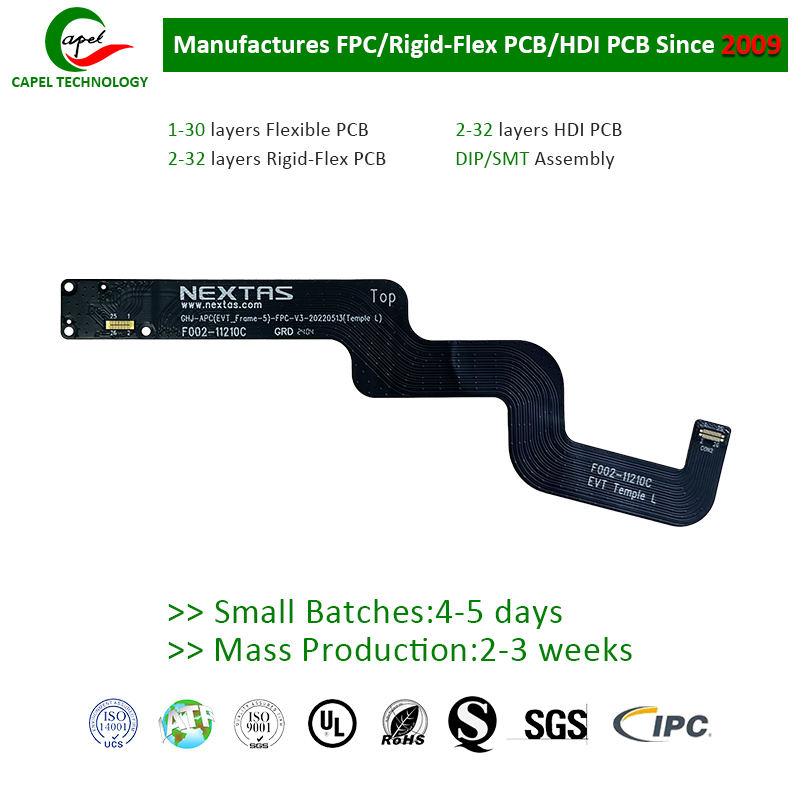
Acabado Superficial: La Importancia de ENIG 2uin
Uno de los aspectos críticos de la fabricación de FPC multicapa es el acabado de la superficie. Una opción común para los FPC de alta calidad es el acabado de inmersión en oro de níquel electrolítico (ENIG), específicamente con un espesor de 2uin. Este acabado superficial ofrece varias ventajas:
Resistencia a la corrosión:ENIG proporciona una excelente protección contra la oxidación y la corrosión, asegurando la longevidad del circuito.
Soldabilidad:La capa de oro mejora la soldabilidad, lo que facilita la unión de componentes durante el ensamblaje.
Llanura:Los acabados ENIG son conocidos por su planitud, lo cual es crucial para garantizar conexiones confiables en diseños multicapa.
Al optar por un acabado superficial ENIG 2uin, los fabricantes pueden garantizar que sus FPC multicapa mantengan un alto rendimiento y confiabilidad durante todo su ciclo de vida.
Grosor del tablero: la importancia de 0,3 mm
El grosor del tablero es otro factor crítico en la fabricación de FPC multicapa. Una especificación común es un grosor de 0,3 mm, que logra un equilibrio entre flexibilidad y durabilidad. Este espesor permite diseños complejos manteniendo la integridad estructural requerida para diversas aplicaciones.
Las placas delgadas son particularmente ventajosas en dispositivos compactos donde el espacio es escaso. Sin embargo, lograr el espesor correcto requiere precisión en el proceso de fabricación para garantizar que el FPC pueda soportar tensiones mecánicas sin comprometer el rendimiento.
El proceso de fabricación: precisión y control de calidad
El proceso de fabricación de FPC multicapa implica varias etapas, cada una de las cuales requiere una atención meticulosa al detalle. Aquí hay una breve descripción general de los pasos clave involucrados:
Diseño y creación de prototipos: El proceso comienza con la fase de diseño, donde los ingenieros crean esquemas y diseños detallados. La creación de prototipos permite probar y validar el diseño antes de la producción en masa.
Selección de materiales:Elegir los materiales adecuados es crucial. A menudo se utilizan películas de poliimida o poliéster de alta calidad por sus excelentes propiedades térmicas y eléctricas.
Apilamiento de capas:En los FPC multicapa, las capas se apilan y alinean con precisión. Este paso es fundamental para garantizar que las conexiones eléctricas entre capas sean confiables.
Grabado y chapado:Los patrones del circuito se crean mediante grabado, seguido de un revestimiento para generar el espesor de cobre necesario.
Acabado superficial:Después del grabado, se aplica el acabado superficial ENIG, proporcionando la protección y soldabilidad necesarias.
Pruebas:Se realizan pruebas rigurosas para garantizar que el FPC cumpla con todas las especificaciones. Esto incluye pruebas eléctricas, pruebas de tensión mecánica y pruebas de ciclos térmicos.
Inspección final y control de calidad: antes del envío, cada FPC se somete a una inspección final para garantizar que cumple con los estándares requeridos. El control de calidad es primordial en el proceso de fabricación para evitar defectos y garantizar la confiabilidad.
Aplicaciones de campo del cable de pantalla de prueba
Una de las aplicaciones importantes de los FPC multicapa personalizados es el campo del cable de pantalla de prueba. Estos cables son esenciales para conectar varios componentes en entornos de prueba, asegurando que las señales se transmitan de manera precisa y eficiente. La flexibilidad y compacidad de los FPC multicapa los hacen ideales para esta aplicación, ya que permiten un fácil enrutamiento e instalación en espacios reducidos.
En aplicaciones de cables de pantalla de prueba, la confiabilidad del FPC es primordial. Cualquier fallo en el cable puede dar lugar a resultados de prueba inexactos, por lo que es fundamental que los fabricantes cumplan estrictas medidas de control de calidad durante todo el proceso de producción.


Hora de publicación: 22 de octubre de 2024
Atrás